CASPER — It takes a lot of horsepower — and manpower — to keep aircraft landing and taking off at the Casper-Natrona County International Airport during Wyoming’s windy and snowy winters.
In many ways, it’s a numbers game. A 400-horsepower truck carries a separate 700-horsepower engine that spins a 24-foot snowblower as it moves down the 10,000-foot runway. As it churns through ice and snow, it sends it flying 100-feet off to the side.
These are serious machines.
Jake Hlavacek, the airport’s deputy director for construction and maintenance, said “it takes a village” to ensure the facility’s commercial, medical and international flights can take off and land at their appointed times. And it happens at all hours of any day.
And while weather conditions may ground aircraft from time to time, there’s no way the clearing crew will let the runways go.
“I don’t know if I can remember a time we have closed the airport due to the runways being in poor condition,” he said. “We pride ourselves very much on the fact that we never want a commercial flight to not go out on our account. The majority of the time, 95% or more, it’s not because the surfaces are closed in Casper, it’s the destination is having issues, whether it is Denver or Salt Lake or something like that.”
Wide Runways
But make no mistake, keeping the 150-foot-wide runways safe for airplane tires to touchdown on or take off from can be extremely challenging.
Hlavacek said his 11-member crew of maintenance workers that handle carpentry, plumbing, electrical and grounds upkeep at the 140 airport buildings double as the snow removal crew. They are responsible for the two runways, taxiways and parking area for aircraft behind the flight line fence as well as all the roads and parking areas on the other side of the fence.
The airport is like a mini-city with some manufacturing areas, oil field-associated firms, some residential housing and a historical area that contains row upon row of former barracks for the old airbase that trained bomber crews during World War II. Those buildings now are used for rented storage.
The equipment used on the airfield proper is a lot bigger than what’s used on the road leading into the airport parking lot or adjacent streets.
“The airport equipment is a lot different than city streets. Most of their plows are 12 feet wide,” Hlavacek said. “Ours are anywhere from 20- and 24-foot wide, just the plow itself. We are not regulated by DOT to fit in lanes. The bigger the equipment, the better for us. The quicker we can clear surfaces.”
Monster Machines
Crews working the airfield have at their disposal two plow broom-combos that consist of a front part plow and a middle part broom, five plows, one dedicated broom and two airfield snowblowers. They are getting ready to order a third snowblower with a price tag of $914,000. Those who work the parking lots and streets have standard plows, frontend loaders, tractors and snowblower equipment.
Even before the snow starts to fly, the crew is watching weather forecasts and preparing to mobilize. When the snow starts to fly, two plow-and-broom combination machines typically start work on the runways and put the snow into windrows that will be churned up and spit out 100 feet away by the blower.
“With runway lights you are not able to just plow things off the side because you are going to cover them up or knock them over. Everything on an airfield is frangible. From lighting to signs, everything is designed so that if it is hit, it will break away,” Hlavacek said. “You want to save the aircraft and sacrifice the light.”
Three Inches, 14 Hours
Just 3 inches of snow will take the crew members using all their equipment about 14 hours of work to clear. Priorities are the main runway, a taxiway, the FedEx area, and on the outside of the airport the parking lot and entry and exit roads.
When a storm started dumping more than 30 inches of snow on the airport last winter, Hlavacek said the crews did what they could.
“Last year we got hammered. That one was tough,” he said. “We were able to keep the runway open, a primary taxiway and a then pretty much a pathway to the terminal, and that was all we could maintain to allow the commercial aircraft to go out.”
Three members of his team are assigned to the area outside the flight area, and eight to the runways and areas used by aircraft. Each operator within the flight space depend on their radios, one that communicates with the control tower and another to communicate between themselves.
Dangerous Work
During high winds and off hours, the work can be dangerous. To mitigate the risk, crew members all travel the same direction on the runway and stay in contact with each other and the control tower. During times the control tower is empty, they broadcast their presence on the runway to the aircraft frequency to ensure a flight does not land on top of them.
When weather hits, it often is an early morning call — a FedEx flight arrives around 4:30 a.m.
“The guys are typically called about 2:30 in the morning and they are here as long as they need to be get the job done. Sometimes we are here for 20 hours straight,” Hlavacek said. “There have been times we have been out here at 2:30 in the morning and plowed to midnight, went home and got a couple of hours of sleep and back here at 3 a.m. to get the runways open.”
Under FAA rules, which prescribe the equipment needed, how it is stored and the manpower to run it based on the size of the airport, his team has an hour to get the main runway cleared.
Lockers And A Shower
There are lockers, a shower and sleeping quarters for the crew if need be. On long days, Hlavacek said airport staff will provide breakfast and other morale boosting measures to keep the team going.
The maintenance crew works closely with the operations side of the airport that handles policing, firefighting, medical issues and security. A member of that team is assigned to drive the runways with a special device that measures friction and resistance on the surface of the runways.
If the resistance does not meet FAA regulations, the maintenance team is sent out with snowplows, blowers, brooms, deicing equipment or whatever else is needed to bring the runway into compliance.
“Whether it is water, ice, slush, snow — anything of that nature we take care of,” he said.
Hockey-Puck Sensors
In addition to the National Weather Service, the airport uses its own weather equipment to track when the maintenance team needs to launch. There are hockey puck-sized sensors embedded in the runways that feed wind speed, moisture, and temperature data to airport personnel.
“That tool we use quite heavily and then we can know when surfaces are going to freeze over,” Hlavacek said. “Sometimes we opt to pretreat a runway as a preventive measure to keep the ice off, using liquid or pellet deicer.”
The airport keeps about $50,000 worth of deicer on hand in 14 1-ton bags of pellets made of sodium acetate and gallons of liquid potassium acetate. Sand and salt are not allowed because of their potential to damage aircraft.
Animal Prevention
Snow is not the only adversary for the team. In the summer months, the crew has to keep the grass down to under 4 inches to help prevent animals from being attracted to the airfield area. Hlavacek said longer grass allows for worms, which attract birds, and then coyotes.
But sometimes wildlife finds a way to get in. More recently it has been turkeys and antelope. Years ago, a bull elk and even a bear have made an appearance at the Casper airfield.
Tactics to remove the animals include trying to push them off from the airfield area through a fence. If that does not work, the operations team is allowed to use lethal means.
One member of the grounds team spends 40 hours a week just continually mowing the runway and flight line areas.
While the hours can be long, Hvalacek said he enjoys coming into work every day.
“I love it and there is something different every day,” he said. “There is always a new challenge.”
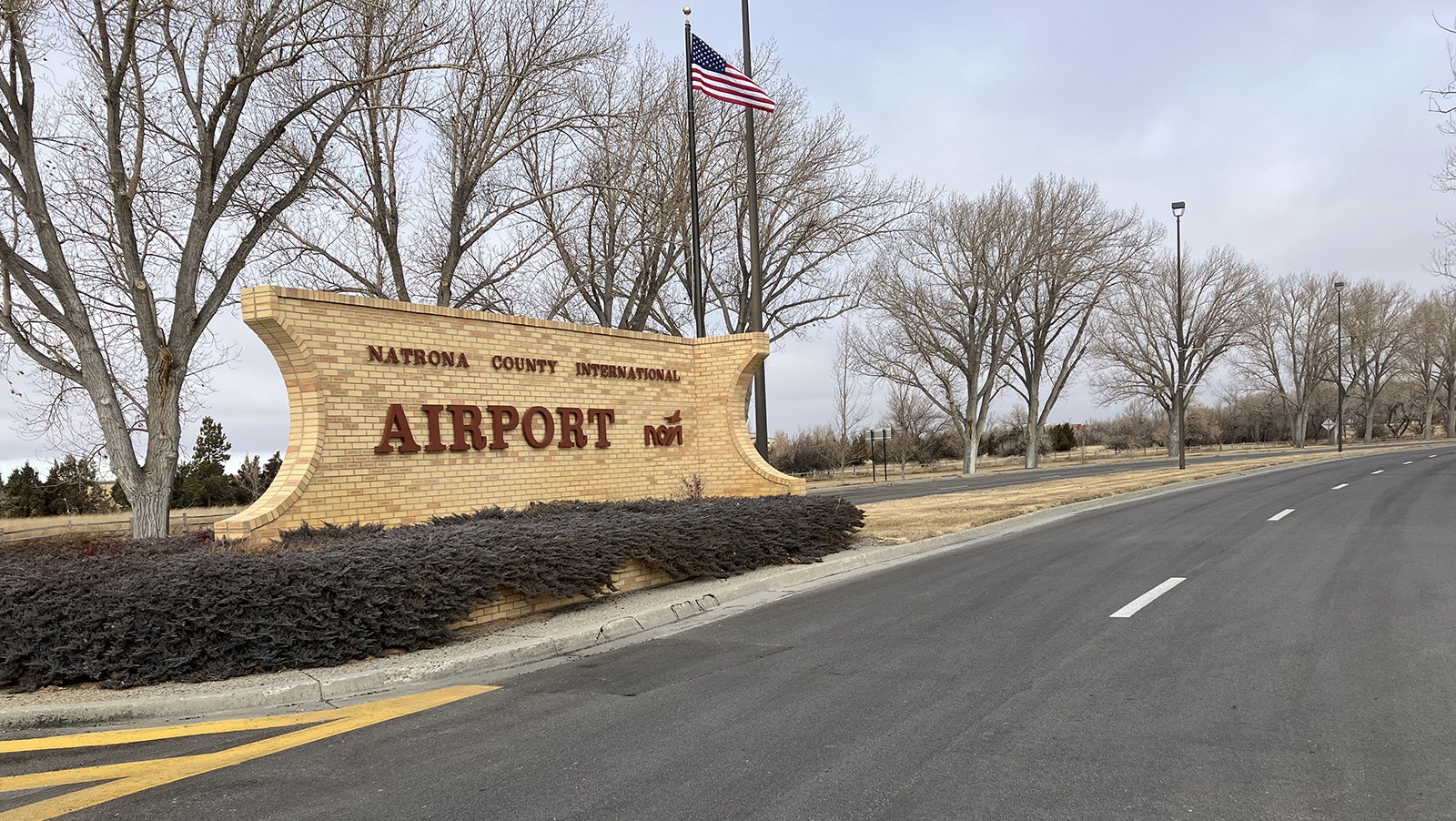
Dale Killingbeck can be reached at dale@cowboystatedaily.com.