By Renée Jean, Business and Tourism Reporter
renee@cowboystatedaily.com
L&H industrial makes some of the world’s largest parts, reaching far beyond Wyoming with innovative mechanical solutions that are now exported around the world. The multimillion-dollar company has built parts for NASA that have been in outer space.
Now the Gillette-based company wants build parts for “inner” space as well, leveraging the atom as a source of energy.
Company officials confirm they have been romancing the nuclear power industry of late and, with that sector appearing to find a more favorable atmosphere these days, the company believes it is poised to break into a nuclear sector that’s focused on building smaller plants across the nation.
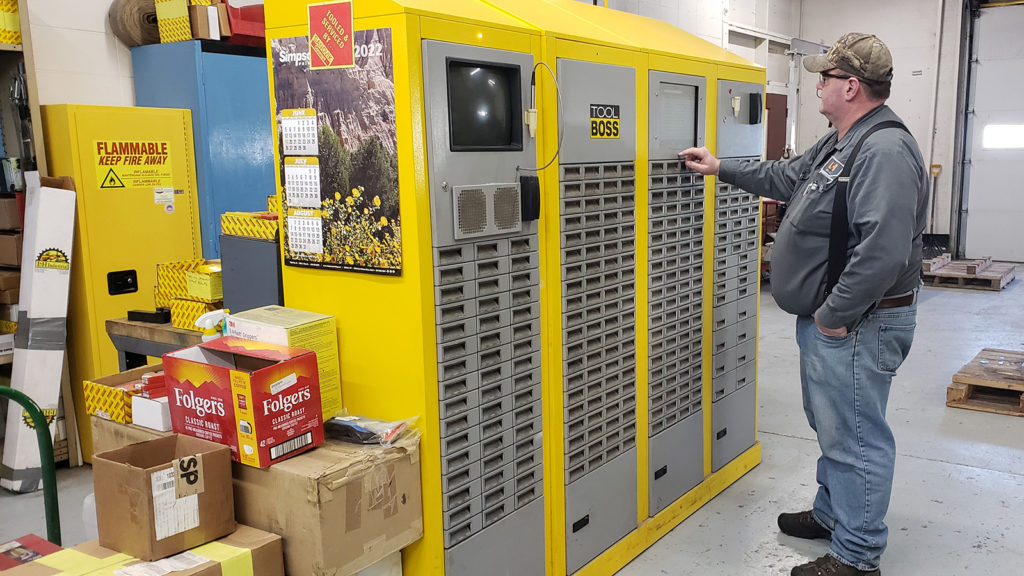
Began Small
L&H has 387 employees across North and South America, with field offices all across the United States.
It’s also considering expansions to improve what it can do in important markets like Canada, and exports its engineering and machined solutions around the globe.
But it wasn’t always so. In the beginning, L&H was a very small oil field service company, with just six employees and an awful lot of of broken oil rig parts and rusty gears laying in piles around the shop, which was located on Douglas Highway near the railroad tracks.
Leon Wandler was the “L” in L&H, while Hank Barney was the “H.” The two bought the nearly bankrupt shop during the 1960 oil boom in Gillette.
Just A Business
At first, L&H was focused on making a little money to keep Wandler’s family going, L&H Vice President of Sales and Marketing Dustin Roush told Cowboy State Daily.
“He loved the oil field and, when he bought that shop, those guys didn’t think like that back then,” he said when asked about Leon Wandler’s original mission. “They didn’t think about missions and values.
“He always wanted to work for himself. It was just about, ‘I’m gonna buy this shop’ and, you know, he was a machinist by trade.”
The shop’s focus was odd machine shop jobs for the oil field — mainly rebuilding pipes and fixing workover and drilling rigs.
But Wandler had a quick mind and an excellent grasp of engineering. He often came up with solutions where others saw problems.
That allowed him to quickly establish a good reputation within the roughneck environment that characterized the time period, and he was able to build a new shop in the 1980s.
Right after the new shop was done, however, oil crashed. Wandler had to sell off other business interests to save his first love, L&H, which was the heart of all his businesses.
“He almost went bankrupt, and he had to go work for the mines,” Roush said. “That’s what forced us into the mining industry. He did not want to go to work for the mine, but the oil was done. He had to have a new outlet, a new source of income.”
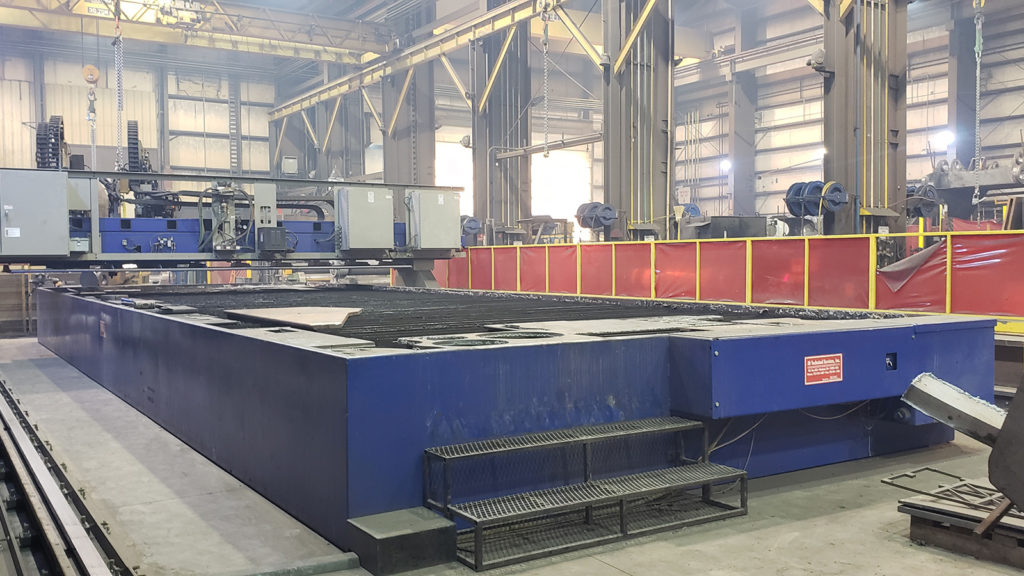
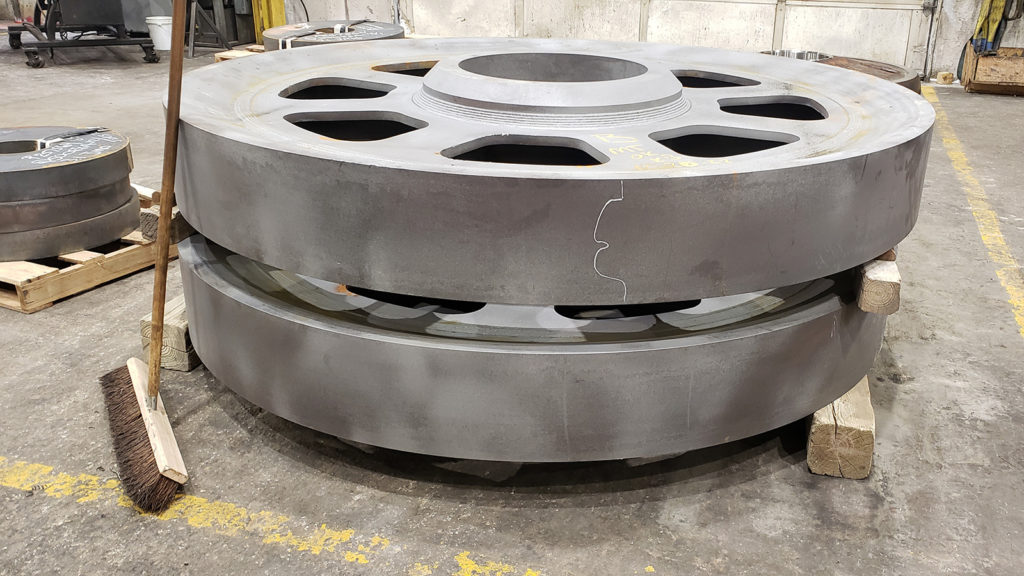
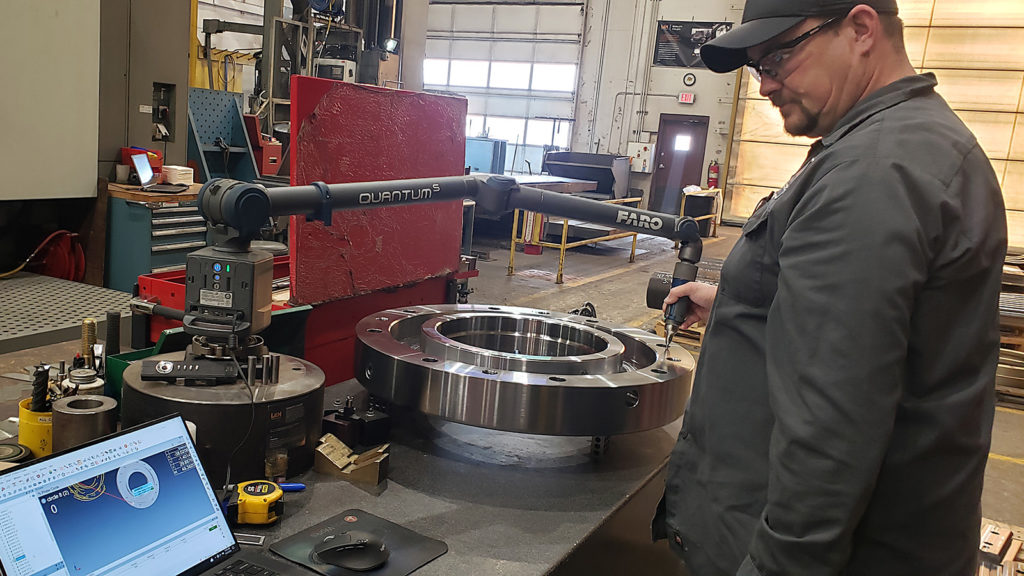
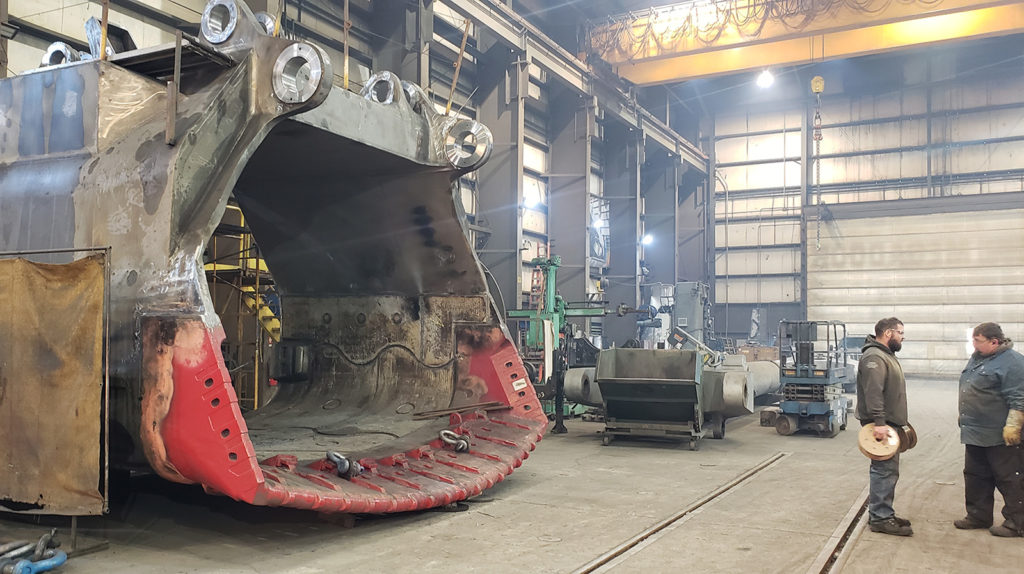
Culture Was Different
Those days were a different time, Roush said.
“There were no worries about drug policies,” he said. “You know, it was just, ‘We have a job in front of us. Let’s go get it done.’”
Some of the machinists then were even known alcoholics, Roush said.
“They would literally come in and they might be, you know, a little buzzed or hungover from the night before,” he said. “They said one guy would come in there and he walked over to an oxygen bottle and, you know, stuck his mouth on it and took a hit off the oxygen bottle because he was hung over.”
Push To Modernize
When Roush’s uncles bought the company, modernizing the entire culture was one of their first challenges.
“It took a long time, but we put a lot of focus on safety because of our employees,” Roush said. “We want to make sure everybody ends up going home, so safety’s always at the forefront of what we do every day.
“We want to make sure everyone goes home alive, with all their digits and their eyeballs.”
The company hasn’t, however, adopted any particular certified safety programs. True to its innovative nature, L&H has paved its own path.
“We’ve taken what we think are best practices and we’ve used little bits and pieces from all these programs and melded them together to fit our facilities in our shops,” Roush said.
Going Nuclear
On a recent tour by someone who vets companies for the nuclear industry, Roush said the representative was “blown away” by the safety culture at L&H and told them the company is “poised” to break into the sector at last.
Mike Wandler has been leading the company’s exploration of opportunities in the nuclear sector for many years, seeking to find a comfortable niche for L&H engineers.
“It was kind of confusing as to where the opportunities were,” he told Cowboy State Daily. “But now I’ve kind of found it. It’s in the supply chain. So for me and other innovative Wyoming entrepreneurs, that’s feeding into the supply chain as nuclear energy becomes commercially viable.”
Wyoming has been bringing in nuclear power professionals to the Cowboy State to show leaders in the nuclear sector that there are opportunities for growth in the Cowboy State, which, like neighboring Montana and North Dakota, is also friendly to an all-of-the-above energy strategy.
Wandler has been acting as lead for the private sector in that statewide effort.
“I go out and I help them find, you know, if it’s not me and my manufacturing capabilities, I help them find somebody they can work with,” he said. “So, it’s all of the people doing small modular reactors, nuclear batteries.”
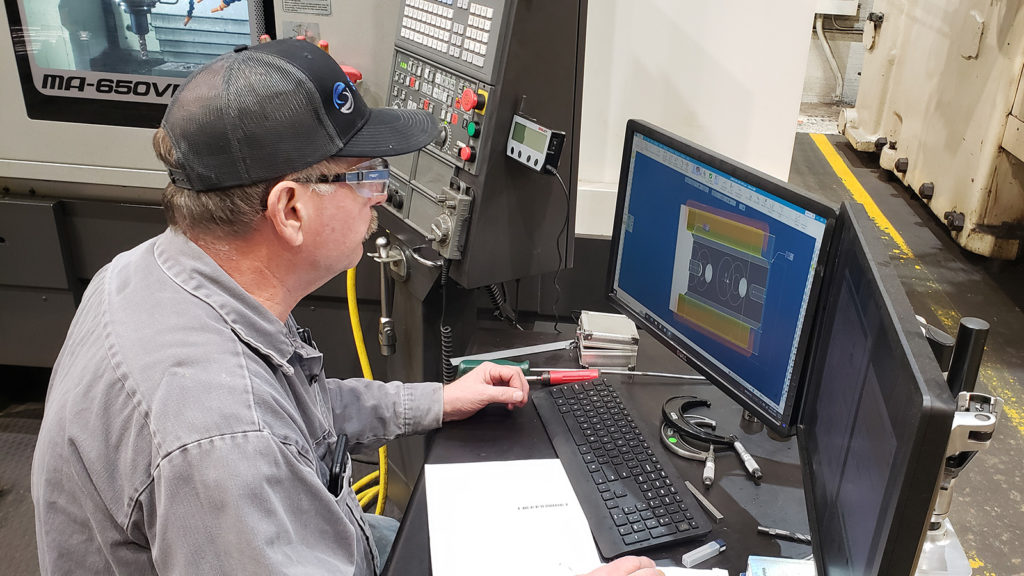
Smaller Is Sometimes Better
Smaller reactors are the direction the nuclear industry is headed, Wandler said.
Many small reactors operating across a power grid create a more resilient network than one large multi-state plant. The safety parameters are stronger, too.
In fact, Wandler has done a deep dive into the safety of these smaller plants.
“They’re only doing incredibly safe designs that are, what do they call it, they basically cool down,” Wandler said. “They don’t take any exterior powers. They don’t have to have generators. They’re convection-cooled, so even if they were completely flooded, they’ll just stop and cool down naturally with no human intervention whatsoever.”
The designs are engineered to prevent incidents. And, with the smaller size, even if a problem did happen, it would be on a much smaller scale than a Fukushima or Chernobyl.
Getting in on the ground floor of building out this new vision for the nuclear power industry is one way L&H hopes to find a new niche and diversify.
“They need parts to put these things together,” Wandler said. “And then they need services to install and maintain them. That’s the supply chain part. So that’s how we’re going to keep jobs and keep growing manufacturing revenues.”
Making Smart Parts
But it’s not just nuclear and other energy industries where L&H is working to diversify.
The company also is working on so-called “smart” components, Roush told Cowboy State Daily.
These components will have sensors that “talk” to the data cloud, and then software analysis can help pinpoint from that data which parts are getting tired and run down.
“We have our first field test going on right now,” Roush said. “And it went off without a hitch. We really believe that that’s going to be the next thing that we’re diving into is making our components smarter.”
While L&H’s current field test is geared toward mining components, the principles are generally applicable to all kinds of other mechanical components. Roush believes this will ultimately help the company diversify into other manufacturing sectors.
“We’ve got a platform that is, basically speaking, we’re going to shoot all this data and information backups to the cloud,” Roush said. “It’s available to the customer if, they, you know, if that machine goes bump in the night, then it alerts their phone or alerts whoever they want to direct it to.
“That way, proper maintenance can get in there and at a least trouble shoot.”